Quality Assurance Group
The Quality Assurance (QA) group conducts audits to ensure compliance with TCEQ programs and projects are in accordance with the Quality Assurance Project Plans (QAPPs).
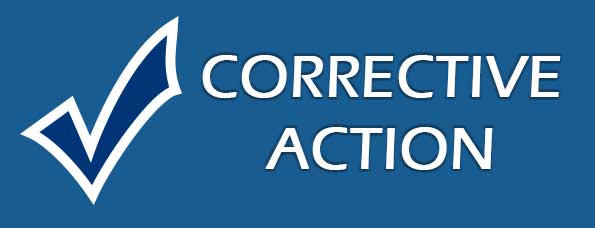
The corrective action process is a tool to identify and fix nonconformities in a system that, if not corrected, may have a negative impact on project deliverables.
Identification of Quality System Nonconformities
- A nonconformity is defined as any unauthorized deviation from acceptable procedures or practices, a defect in an item, or failure to conform with a specified requirement.
- Nonconformities may be identified during a formal agency audit or internal audit. Nonconformities may also be self-identified during routine work.
- Nonconformities shall be documented immediately and reported to supervisory personnel in writing. The reports of nonconformities to supervisory personnel will serve as initial nonconformity notices.
- Lead QA staff shall determine whether or not nonconformities are significant conditions as defined in the TCEQ QMP, including cases in which nonconformities recur after having been identified and previously corrected.
- Lead QA staff shall notify affected Deputy Directors, Section Managers, Grant and Program Managers, and the QA Manager of any significant conditions.
- If lead QA staff and project, program, or organizational management disagree as to the determination of significant conditions for a nonconformity, any of the parties may appeal to the TCEQ QA Manager for resolution.
Planning and Implementing Corrective Actions
- With concurrence of affected lead QA staff, Project Managers or designees shall prepare a corrective action plan (CAP) to determine and document the following with regard to each nonconformity:
- root cause(s);
- programmatic impacts;
- required corrective action(s);
- required corrective action(s) to prevent recurrence;
- means by which corrective actions will be verified as effective;
- means by which corrective action completion will be documented;
- timetable(s); and
- individual(s) responsible.
- Within 30 days of the initial nonconformity notice, the project manager or designees shall submit forward copies of CAPs to supervisory and lead QA staff involved in implementing or monitoring corrective actions.
- Lead QA staff shall forward copies to appropriate personnel per the QMP.
- Supervisory staff shall ensure CAPs are implemented effectively and in a timely manner. Lead QA staff may monitor the implementation of CAPs and shall advise the appropriate project and program manager if the plans are not implemented in a timely manner.
- Depending upon program requirements, either the Project Manager or QA staff will notify affected management and the lead QA staff when corrective actions have been completed and verified to be effective, and that the associated CAP(s) can be closed.
- In the case of significant conditions, lead QA staff shall advise the appropriate personnel per QMP if CAPs are not implemented in a timely manner.
- In the case of significant conditions, the lead QA staff shall advise the appropriate personnel when corrective actions have been completed and verified to be effective, and that the associated CAP(s) can be closed.
- The External Corrective Action Response Form must be used by a Program to respond to a nonconformity identified during their TCEQ assessment.
- The External Monitoring Form must be used by a Program to respond to a significant nonconformity identified during their TCEQ assessment.
- Instructions and guidance for completing the CAR form and addressing C.A.s effectively: TCEQ QA CAP template
A QAPP is a formal document that describes in comprehensive detail the necessary quality assurance, quality control, and other technical activities that must be implemented to ensure that the results of the work performed will satisfy the stated performance criteria.
Drafting a New QAPP
- QAPPs shall be drafted, with the assistance and involvement of all relevant Program and QA staff, to meet the requirements contained in the current version EPA's QAPP Standard (CIO 2105-S-02 ).
- All participating organizations are given 30 days to review the initial draft and provide comment.
- To avoid delays in project initiation, the QAPP should be submitted to TCEQ Project Managers at least four months before the planned start date (especially for QAPPs requiring EPA approval) unless other arrangements have been made.
- No work covered under the QAPP shall begin until the QAPP has been fully approved with signatures affixed.
Amending a QAPP
- Amendments to QAPPs are developed and approved to reflect changes in project organization, tasks, schedules, objectives, and/or methods; address nonconformities; improve operational efficiency; and accommodate unique or unanticipated circumstances. These changes will remain in effect until the next revision of the QAPP.
- Amendments are effective immediately upon approval by the TCEQ Project Manager or designees, the Lead QA Specialist, the TCEQ QA Manager (or designee), and the EPA Region 6 Project Officer (when required).
- Amendments to QAPPs and the reasons for the changes shall be documented by the TCEQ Project Manager and distributed immediately to all individuals and organizations contained in the QAPP distribution list.
- Amendments shall be incorporated into a revised QAPP during the anniversary revision process, or within 120 days of the QAPP's approval in cases of significant changes. For multi-year QAPPs, amendments must be attached to and noted in annual certification submissions.
Annual Certification of a Multi-Year QAPP
- Multi-year QAPPs for EPA-funded programs and projects must be reviewed annually by the appropriate TCEQ Project Managers or Lead QA Specialist.
- Reviews must be documented and include the relevant signatures to certify the review’s accuracy as well as copies of any program or project changes which were approved via amendment during the prior year.
- If the annual certification process reveals the need for amendments to be made to the project, these should be approved by the EPA (or TCEQ QA Manager for delegated programs) before the completion of the annual certification.
- Any minor administrative changes that will not have an impact on data or operations (e.g., organizational changes, schedule changes not affecting the project design or quality or quantity of work to be performed, etc.) shall also be included as part of the annual certification.
- TCEQ Project Managers or designees must provide certification of the annual reviews to the TCEQ QA Manager and the appropriate EPA Region 6 Project Officer 30 days before the annual anniversary date.
QAPP Revisions and Reissuances
- Until the work outlined in the QAPP is completed, the QAPP shall be revised as necessary and reissued by its expiration date or revised and reissued within 120 days of significant changes, whichever is sooner.
- If the entire QAPP is current, valid, and accurately reflects the project goals and the organization's policy, the reissuance may be done by a certification that states that the plan is current and includes a copy of new, signed approval pages.
QAPP Approval Timetable
- Unless other arrangements have been approved, new QAPPs, including annual and multi-year QAPP updates, shall be prepared and approved according to the following timetable.
Activity Office/Organization | Timetable |
---|---|
Submittal for TCEQ QA review | 135 days before project initiation/ QAPP expiration date |
TCEQ Approval/Submittal to EPA | 75-90 days before project initiation QAPP expiration date |
Comments/ Approval from EPA | 15 days before project initiation/ QAPP expiration date |
For additional information regarding the preparation, review, approval, and distribution of QAPPs, please reference Appendix F of the TCEQ QMP.
Guidance Documents EPA has developed several documents which contain requirements and guidance to assist in the development and implementation of quality systems for both EPA and non-EPA organizations.
These documents include:
- Environmental Information Policy, Procedures and Standards
- Quality Assurance Project Plans Standard (CIO 2105-S-02)
- Guidance on Systematic Planning Using the Data Quality Objectives Process (EPA QA/G-4)
- Guidance for Quality Assurance Project Plans (EPA QA/G-5)
- Guidance for Geospatial Data Quality Assurance Project Plans (EPA QA/G-5G)
- Guidance for Quality Assurance Project Plans for Modeling (EPA QA/G-5M)
- Guidance for Preparing Standard Operating Procedures (EPA QA/G-6)
- Guidance on Technical Audits and Related Assessments for Environmental Data Operations (EPA QA/G-7)
- Guidance for Data Quality Assessment
Demonstrates how to use data quality assessment in evaluating environmental data sets and illustrates how to apply some graphical and statistical tools for performing DQA.
For additional documents, see US EPA Agency Wide Quality Systems Documents .